If you love twists and turns, you can’t do much better than The Scramble. This amazing, four-story vertical adventure with its one-of-a-kind spiral slide just opened June 7th at Minnesota Children’s Museum in St. Paul. Yet, there’s also a thrilling, behind-the-scenes story about what it took to get the 17-foot slide from Germany to the Twin Cities in time for the museum’s grand opening.
In early 2017 when this story began, the museum was nearing the end of a lengthy expansion and renovation project. Before the renovation, many exhibits had not been updated since the museum opened in 1995. And so, over nearly 18 months of construction, the museum worked to add 35 percent more space (from 65,000 to 74,000 square feet), an updated rooftop experience, and an outdoor exhibit.
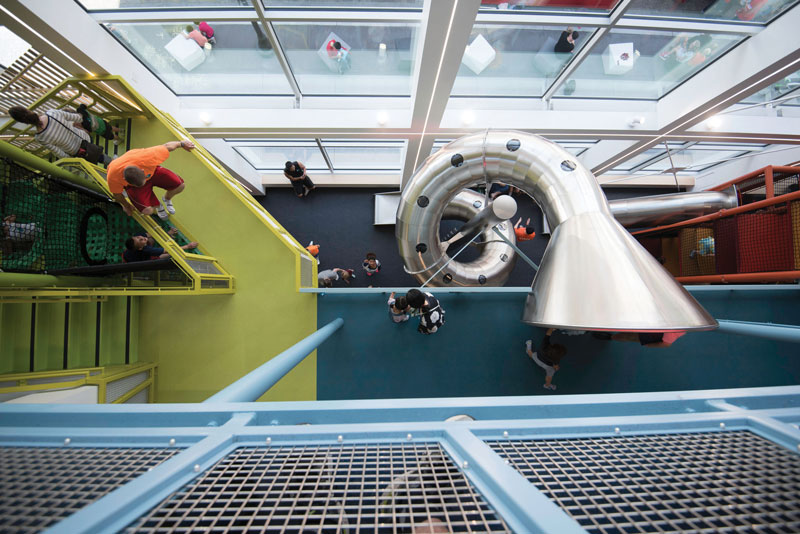
The Scramble was also part of the expansion. The four-story climbing adventure, to be installed behind a new glass façade at the front of the building, included towers and catwalks made of netting, as well as a magnificent spiral slide being manufactured in Germany, one of the few places in the world that could create a customized, stainless steel slide. In order for the slide to be installed within the construction timeline, it needed to arrive by April 28.
Plans were set for the museum’s grand opening and ribbon-cutting ceremony on June 7th. Then, news came from Germany that almost derailed everything. Production of the spiral slide had fallen behind schedule. The new date for the slide’s delivery was May 19—three weeks behind project deadline. This was a potentially devastating setback. The slide had to arrive on time so it could be assembled, installed, and tested. Until all this could be completed, the construction crew could not put the last wall in place to finish the expansion.
Dianne Krizan, the president of Minnesota Children’s Museum, evaluated the options. There was no getting around the deadline for the slide. Unless everything happened according to the original plan, they would have to push back the grand opening by several weeks. The museum’s grand opening date was now in jeopardy.
At this point, the story took another turn. On April 7, Krizan emailed a former member of the museum’s board of directors, Dan Ryan, and explained the situation. Ryan is vice president of North American Surface Transportation at C.H. Robinson, a third party logistics provider headquartered in Eden Prairie, Minnesota. His company happens to be one of the few in the world with the resources, know-how, and flexibility to make seemingly impossible deliveries just about anywhere in the world.
Ryan assured Krizan that C.H. Robinson could help. He quickly enlisted the help of the company’s Frankfurt and Minneapolis offices. Together, they developed a plan to get things back on track so they could meet the project deadline.
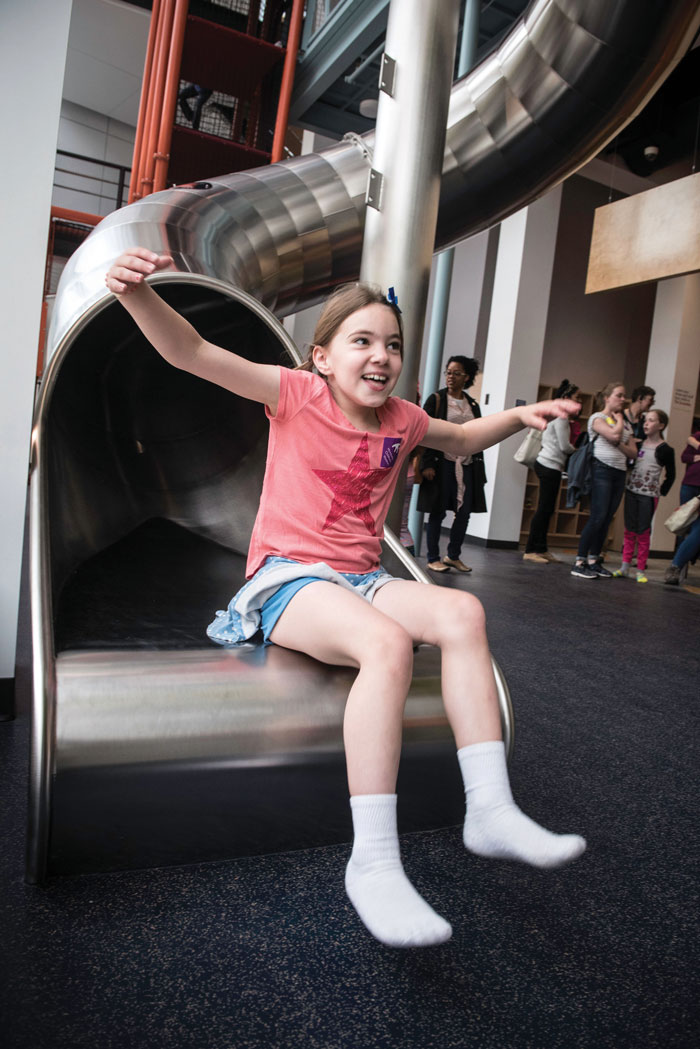
The original plan was to ship the slide by ocean vessel. However, due to the production delay, it was decided to ship the slide by air, making up for lost time.
If this had been an ordinary slide, that might have been the end of the story. But this slide was going to be 17 feet tall. It could not be shipped by air in one piece. The slide had to shipped in large components that could be crated for secure delivery by air. Packing it to prevent damage was the biggest hurdle. C.H. Robinson’s Frankfurt office made all the arrangements with the manufacturer and the airlines.
The Frankfurt team had to work through another complication, too. The components had to be shipped before the Easter holiday, traditionally a very busy shipping time for air cargo to move in Europe. With a lack of air cargo space available, the Frankfurt office got creative. They booked space on two commercial flights—a Boeing 747F and a Boeing 777. They also prepared the documentation to clear the export shipments through German Customs.
Air delivery would cut 24 days off the ocean schedule. That put the slide’s ultimate delivery at four days before the original deadline. In the shipping business, early deliveries can sometimes cause problems of their own. This was a very large shipment, and the packages could not sit there once they arrived. Flatbed trucks would have to navigate through busy downtown St. Paul streets, and the construction crew would have to be there to receive the components early.
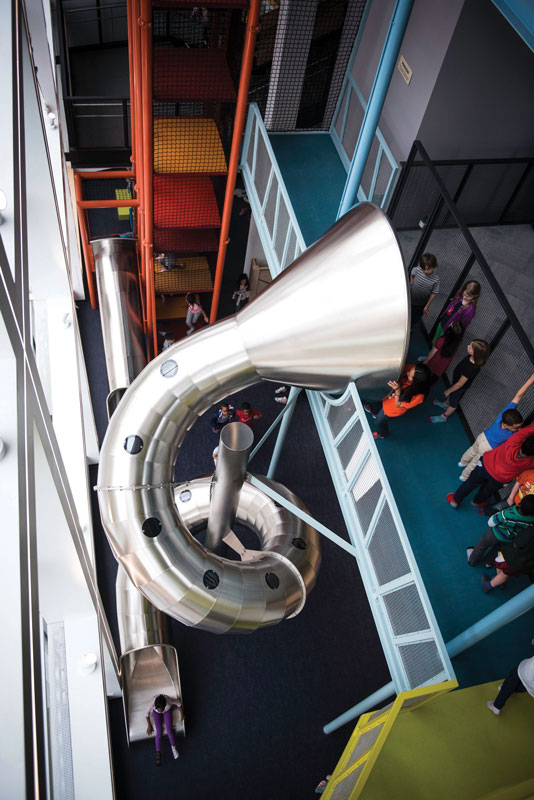
Throughout the entire door-to-door shipping process, C.H. Robinson watched every detail of this shipment on its global technology platform, Navisphere®. This system helped coordinate communications between the manufacturer, the museum, the airlines, the trucking companies in Germany and the United States, and the construction provider so everyone understood what would be required of them, and when.
The planes arrived in the United States, and C.H. Robinson’s Minneapolis International team took control of the details. They coordinated the U.S. Customs clearance, and had flatbed trucks waiting to pick up the shipments. They arrived at Minnesota Children’s Museum on April 24. The slide was assembled as planned, and the museum welcomed its first visitors at the grand opening without a hitch.
As any story about a spiral slide should, this one had a happy ending. Children [and adults] can experience the independence and thrill of The Scramble for years to come. And Minnesota Children’s Museum received an innovative, one-of-a-kind solution for delivery from the dedicated network of global supply chain experts at C.H. Robinson.
Add new comment